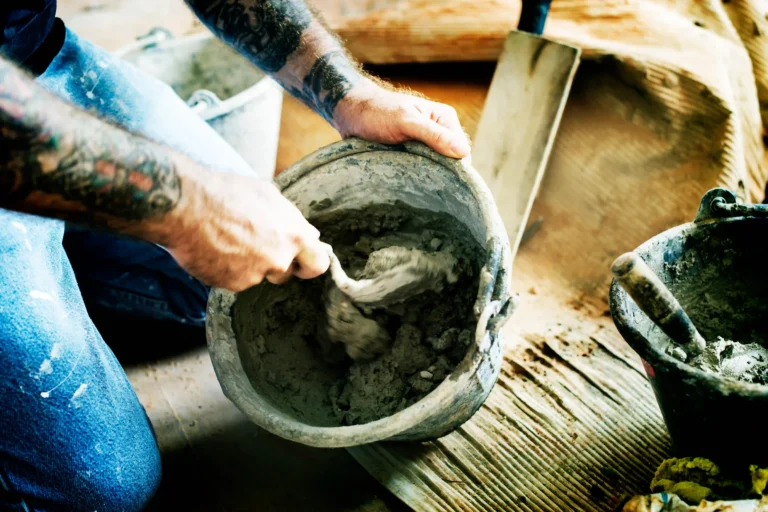
What is Dry Mix Mortar?
- Cementitious binders
- Graded aggregates
- Performance-enhancing mix mortar additives
Comprehensive Dry Mix Mortar Ingredients
1. Binders
Binders are the essential “glue” in dry mix mortar. They create a solid structure by chemically reacting with water. Portland cement is the most common binder, providing high strength and durability. Other binders like gypsum or hydrated lime may be added depending on the mortar type. These materials harden to bind all other components together, forming a cohesive, load-bearing matrix after hydration.
2. Aggregates
Aggregates make up the largest portion (by volume) of dry mix mortar. Fine sand (typically 0.1–1.2 mm) acts as the primary filler, reducing shrinkage and providing mechanical stability. Lightweight aggregates like expanded perlite or vermiculite may replace sand in insulating mortars to lower density. Aggregates create a granular skeleton—their size, shape, and cleanliness directly impact the mortar’s workability, strength, and final texture.
3. Fillers
Fillers are fine mineral powders added to dry mix mortar to optimize performance and cost. Materials like limestone powder (calcium carbonate) or industrial byproducts fill microscopic gaps between sand and binder particles.
4. Functional Mix Mortar Additives
Component | Common Types/Examples | Primary Function | Typical Dosage (wt%) |
---|---|---|---|
Thickeners | Hydroxypropyl methyl cellulose (HPMC) | Water retention, anti-cracking, thickening | 0.1%–0.4% |
Methyl cellulose (MC) | Low-temperature water retention | 0.1%–0.3% | |
Starch ether | Anti-sagging, improved workability | 0.01%–0.05% | |
Polymer Powders | Redispersible polymer powder | Adhesion, flexibility, crack resistance | 1%–5% |
Plasticizers | Polycarboxylate ether (PCE) | High-range water reduction (>20%) | 0.1%–0.3% |
Set Modifiers | Calcium formate | Cold-weather setting, rapid strength gain | 0.5%–2% |
Water Repellents | Silicone hydrophobic powder | Capillary hydrophobization, water resistance | 0.1%–0.5% |
Anti-Crack Agents | Polypropylene (PP) fibers (3–12 mm) | Plastic shrinkage crack control | 0.05%–0.2% |
Functional Aids | Defoamer (silicone/polyether-based) | Air bubble reduction, lower shrinkage | 0.01%–0.05% |
Key Advantages of Dry Mix Mortar
- Excellent Consistency
- Time and Labor Savings
- Minimal Material Waste
- Enhanced Performance
- Broad Application Versatility
Industrial Applications of Dry Mix Mortar
1.Rapid Repair Mortar
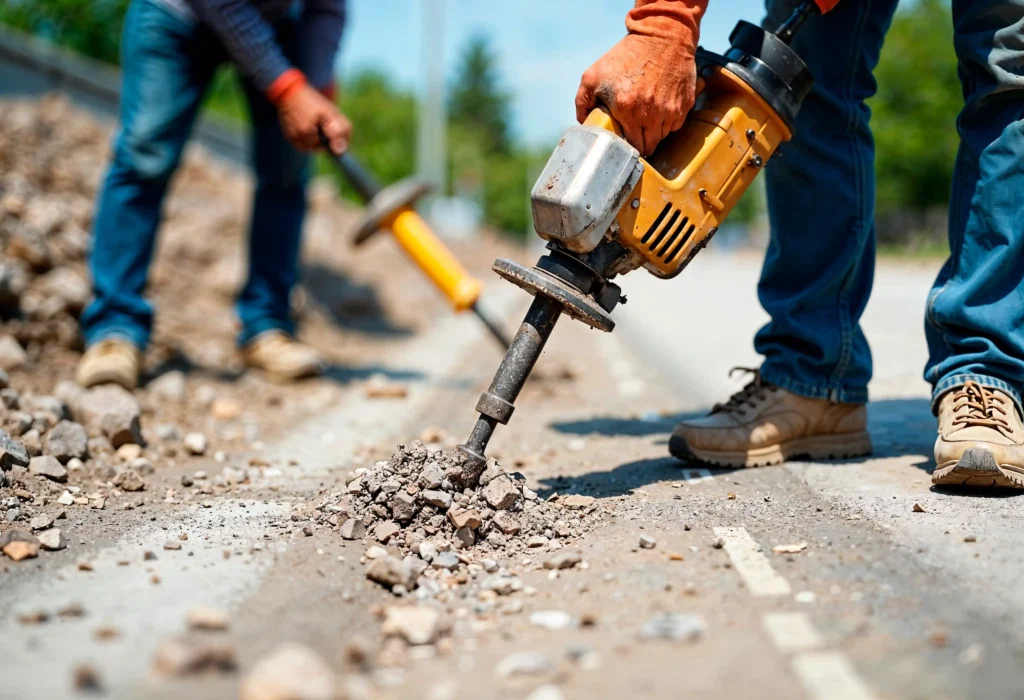
Dry mix mortar enables ultra-fast hardening for road maintenance. It minimizes traffic disruption by completing repairs within hours. Polymer-modified dry mix mortar resists heavy loads and weather extremes, ensuring durable pavement restoration.
2. Tile & Stone Fixing Mortar
Dry mix mortar enables ultra-fast hardening for road maintenance. It minimizes traffic disruption by completing repairs within hours. Polymer-modified dry mix mortar resists heavy loads and weather extremes, ensuring durable pavement restoration.
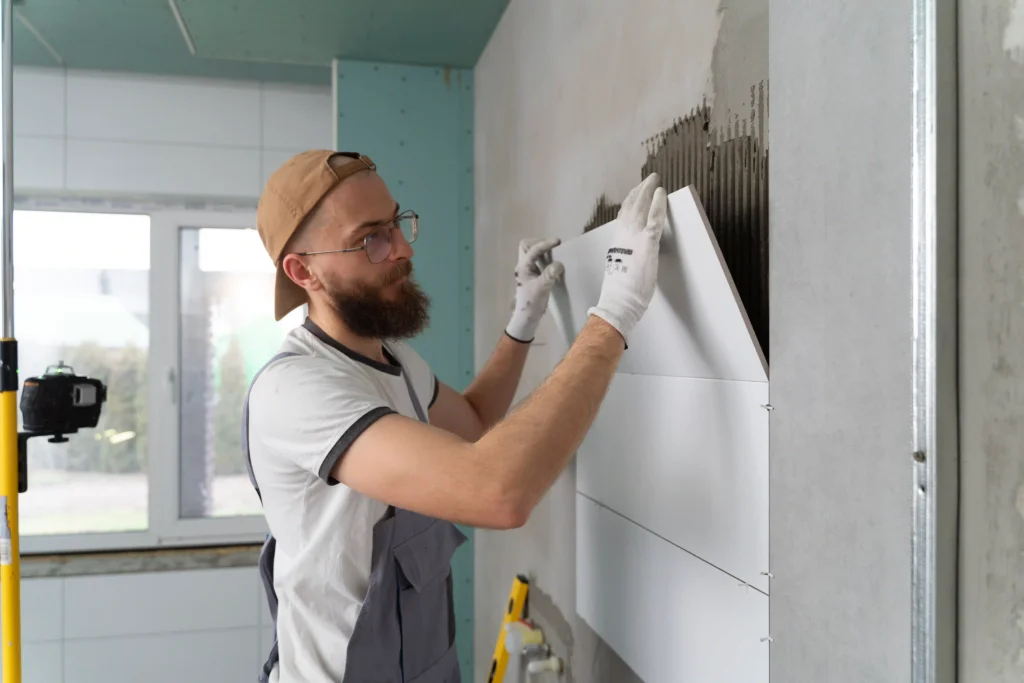
3. External Thermal Insulation Systems (ETICS)
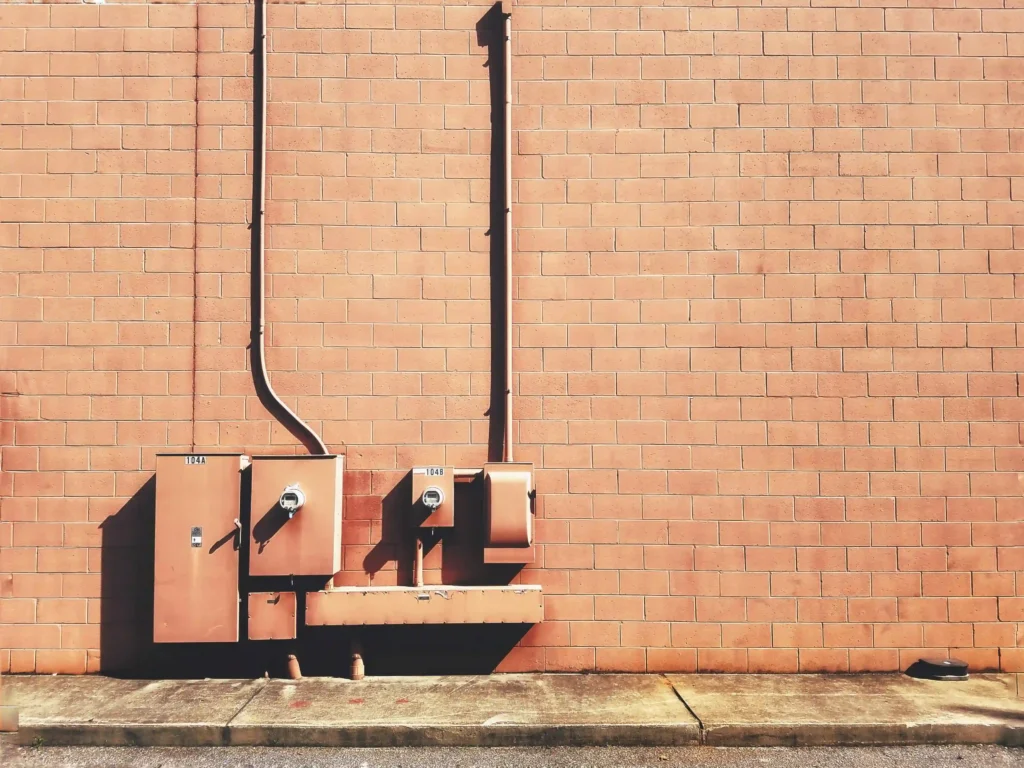
Dry mix mortar bonds insulation boards to building facades seamlessly. Fiber-reinforced dry mix mortar accommodates substrate movement while maintaining weather resistance. This application significantly improves building energy efficiency.
4. Self-Leveling Floor Underlayments
Dry mix mortar creates perfectly flat surfaces for flooring installations. It flows smoothly without manual leveling and dries rapidly to accept finishes. Industrial facilities use dry mix mortar for heavy-duty floor systems.
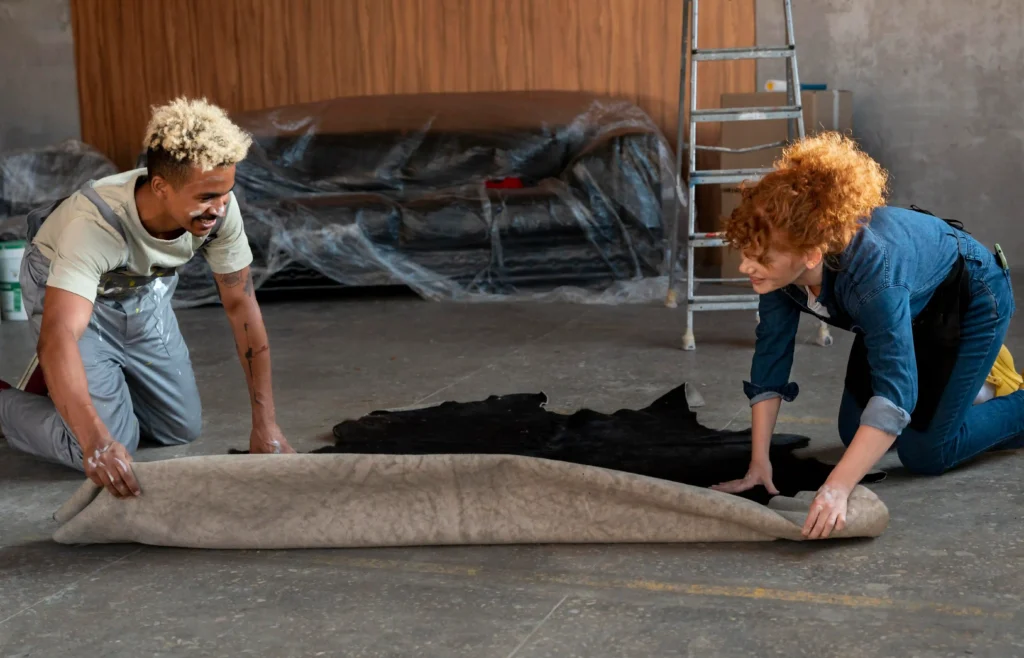
Common Problems & Solutions in Dry Mix Mortar
Cracking during drying
- Cause: Water evaporates too quickly.
- Fix: Add water-retaining additives (like HPMC) to keep moisture longer.
Sagging on vertical surfaces
- Cause: Mortar lacks thickness/stickiness.
- Fix: Use anti-sag agents (e.g., starch ether) for better hold.
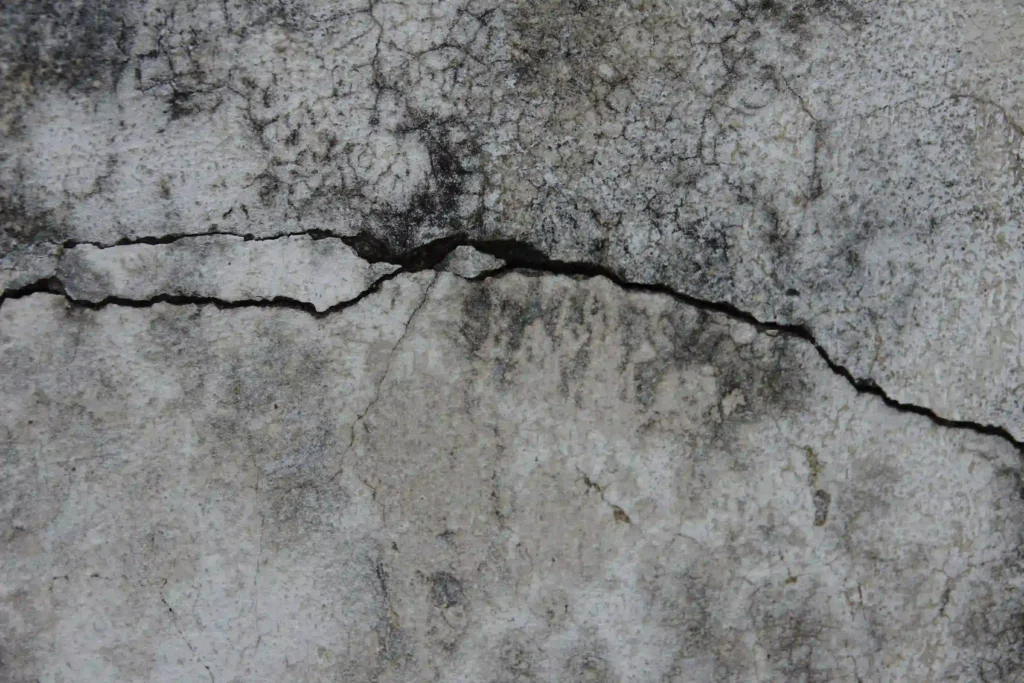
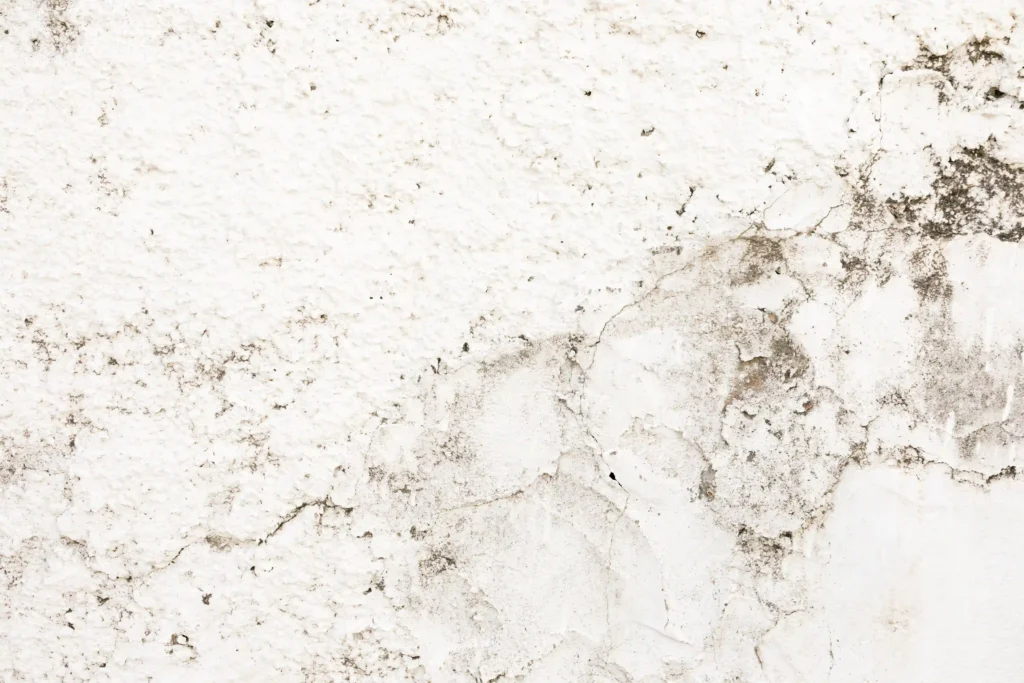
Weak adhesion
- Cause: Not enough bonding strength.
- Fix: Include polymer powders (e.g., VAE RPP) to boost stickiness.
White salt stains (efflorescence)
- Cause: Salts seep to the surface with water.
- Fix: Apply water-repellent additives (e.g., silane) to block leaks.
Poor workability
- Cause: Mix too stiff or clumpy.
- Fix: Optimize with plasticizers (e.g., PCE) for smoother application.
Bubbles in the finished surface
- Cause: Trapped air during mixing.
- Fix: Add defoamers to reduce air pockets.
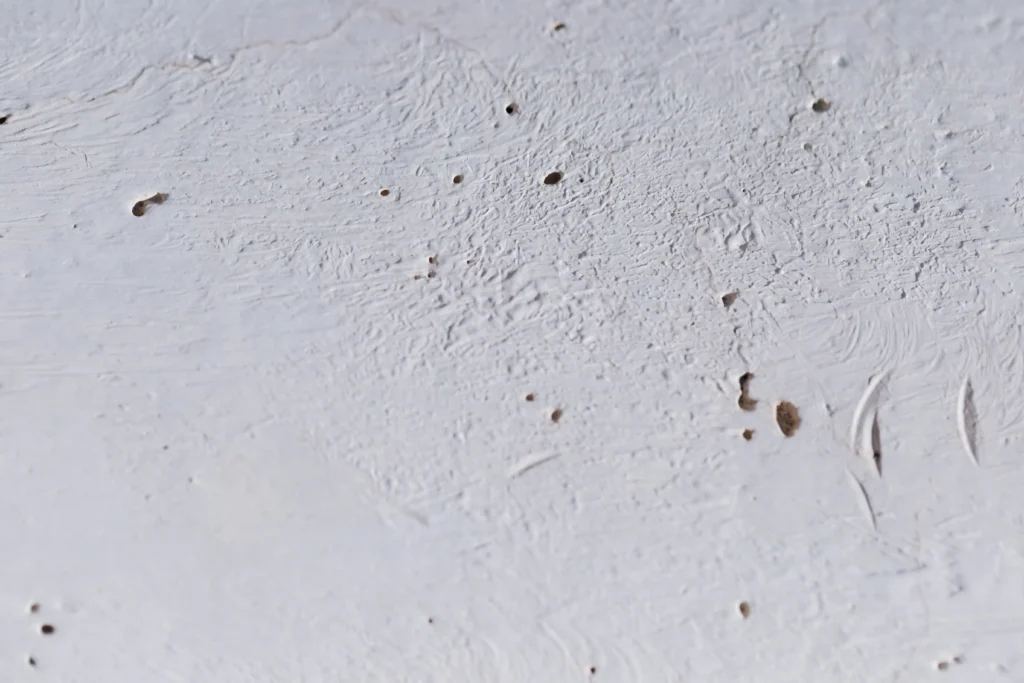
Why Choose Mikazone for Your Dry Mix Mortar Additives
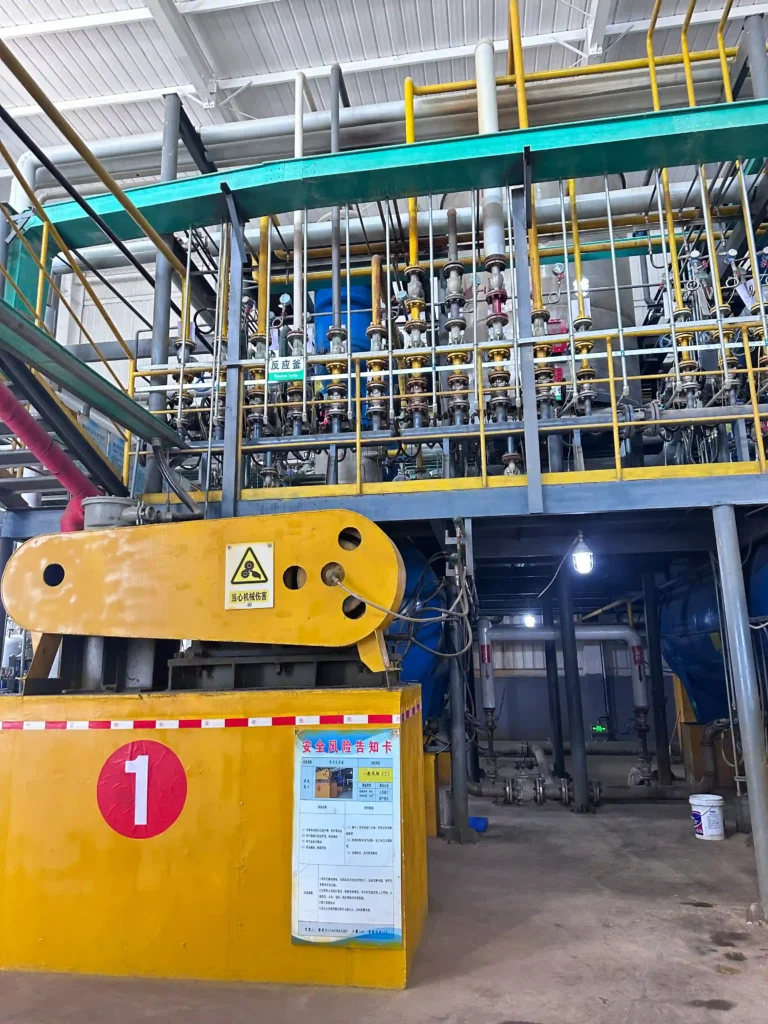
With 3 dedicated factories and 2 WMS-equipped warehouses, we ensure consistent quality and swift delivery of dry mortar additives.
2. Quality That Meets Global Standards
Our ISO 9001-certified facilities ensure every batch of Mikazone product meets:
- Consistent viscosity (±2%)
- <0.5% residue after redispersion
- 99.5% purity levels
3. Application-Focused R&D Support
We manufacture 200+ grades of HPMC and RDP tailored for dry mix mortar applications from tile adhesive to self-leveling underlayments.
Share your dry mix mortar challenges – we develop custom polymer solutions for:
- Extended open time in hot climates
- Sag resistance on vertical surfaces
- Reduced powder dusting during mixing
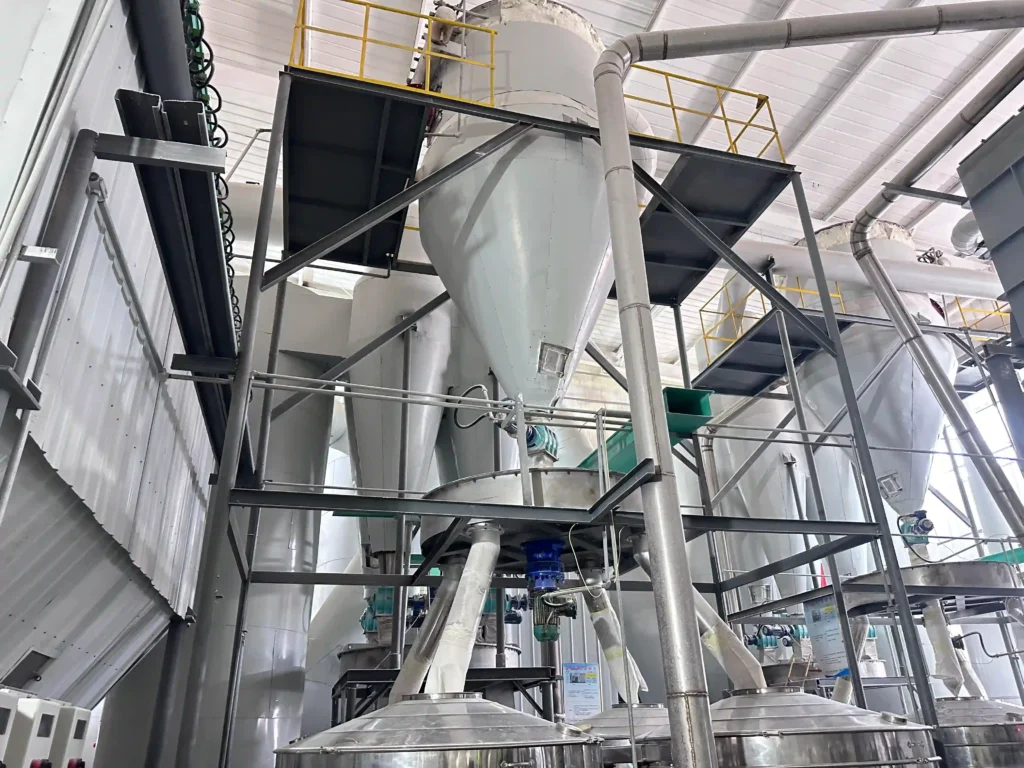
Conclusion
Mikazone empowers dry mix mortar manufacturers to build a competitive advantage through chemistry. Contact us today to:
- Request Free Samples – Test our product in your dry mix mortar formulations
- Explore Customization – We engineer polymers for your specific climate, substrate, or machinery requirements
- Schedule Technical Training – Master polymer optimization in dry mix mortar
Contact Mikazone today to transform your dry mix mortar performance – where science meets construction excellence.