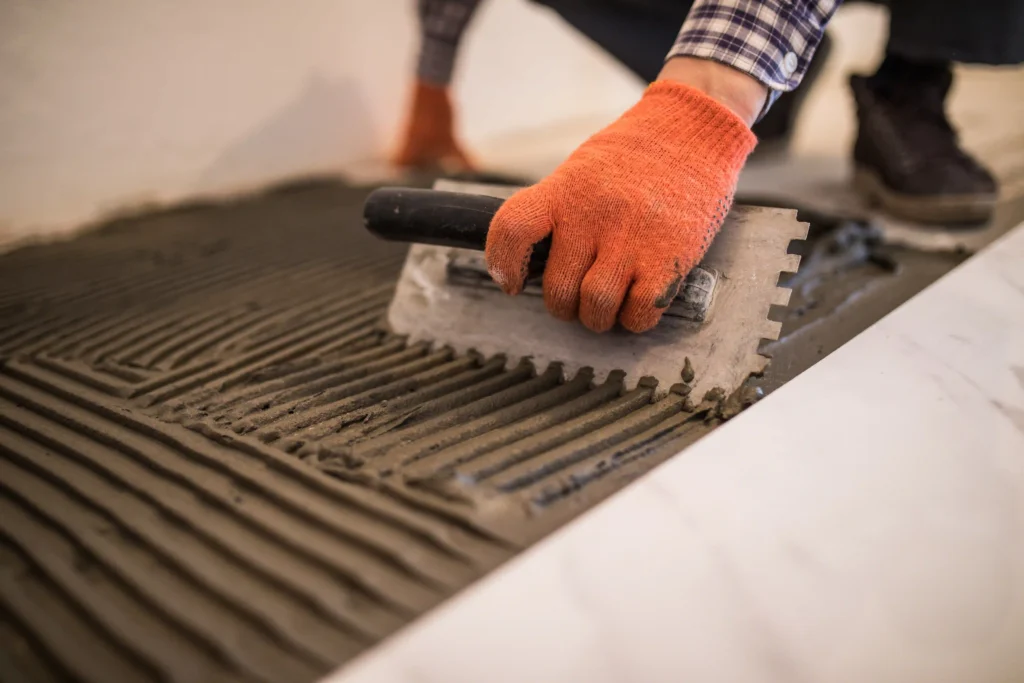
Fast-drying tile adhesive is revolutionizing installation, drastically reducing project timelines and labor costs. Recognizing its critical importance for modern construction efficiency, Mikazone has dedicated significant research to developing a highly efficient formulation. Their breakthrough adhesive sets remarkably fast, enabling grouting within hours. This accelerates project completion, minimizes site disruption, and unlocks new efficiencies for tilers and contractors.
Mikazone’s innovation directly addresses the industry’s need for speed without sacrificing crucial bond strength and workability, making complex or time-sensitive projects significantly more feasible and profitable.
Mikazone's Fast-Drying Tile Adhesive Formulation:
Sulphoaluminate cement: 50%
Quartz Sand (20-40 mesh ): 45%
Hardening Accelerating Admixture: 2%
HPMC (Mikazone®MK40P) : 0.2-0.5%
Redispersible Polymer Powder (Mikavae®MK3510N): 0.5-2.5%
Polycarboxylate Superplasticizer (Mikaultra®PC201): 0.1-0.5%
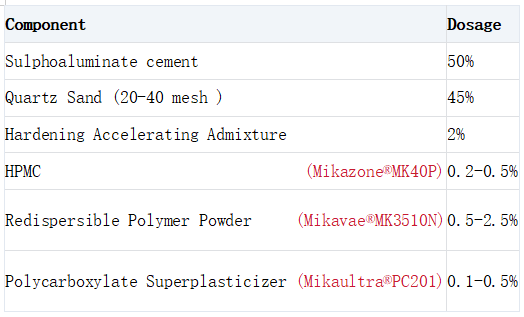
7 Key Components in Fast-Setting Tile Adhesive Formulation
1. Sulphoaluminate Cement
Sulphoaluminate Cement (SAC) is the critical ingredient enabling rapid setting in fast-drying tile adhesives. Its unique chemistry drives exceptionally fast hydration and early strength development. This allows grouting within hours by significantly reducing the adhesive’s curing time.
Compared to Ordinary Portland Cement (OPC), SAC provides the necessary fast track from application to functional use without compromising the long-term bond integrity essential for reliable tile installations
2. Quartz Sand
Quartz Sand is a vital functional filler in fast-drying tile adhesives. This specific coarse-grain size creates a rigid, open skeleton within the adhesive matrix.
This structure efficiently transfers loads, enhances early mechanical strength, and, critically, minimizes shrinkage during the rapid setting phase driven by Sulphoaluminate cement.
The reduced shrinkage prevents crack formation and significantly accelerates moisture release, enabling faster drying and grout readiness while maintaining dimensional stability and long-term bond performance.
3. Hardening Accelerating Admixtures
Hardening Accelerating Admixtures are essential chemical components engineered to drastically shorten the setting and early strength development phase in fast-drying tile adhesives.
They function by rapidly initiating and intensifying the hydration reactions of the cementitious binder (especially Sulphoaluminate Cement), promoting the swift formation of cohesive crystalline structures.
Crucially, hardening accelerating admixtures achieve this rapidity without inducing excessive brittleness or compromising the long-term durability and flexibility of the cured adhesive bond.
3. Hydroxypropyl Methyl Cellulose (HPMC)
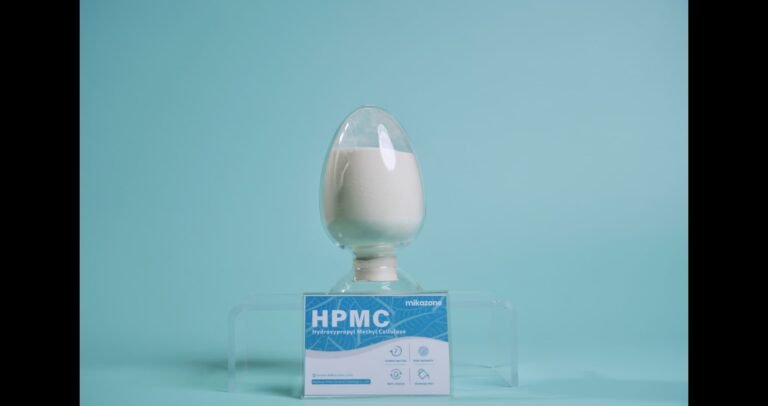
While standard Hydroxypropyl Methylcellulose (HPMC) inherently slows drying, it remains a crucial component in fast-drying tile adhesive formulations. The key is using specially selected HPMC grades (low viscosity, potentially modified substitution) at optimized, often lower dosages, frequently in combination with setting accelerators and desiccants.
This approach leverages HPMC’s essential benefits (initial water retention, workability, adhesion) while mitigating its water-retarding effect to achieve the desired rapid setting, strength development, and early serviceability required for fast-track tiling projects.
4.1 Roles of hydroxypropyl Methylcellulose in Fast-Drying Tile Adhesive
1. Controlled Water Retention
Enables water to escape quickly after initial setting, accelerating drying without compromising early hydration.
2. Precision Workability & Anti-Sag
ensures sufficient wet tack and sag resistance while minimizing water-trapping effects.
3. Acceleration Compatibility
avoids interference with accelerators, allowing rapid cement setting and early strength gain.
4. Enhanced Adhesion Efficiency
Ensures sufficient film formation during the critical early phase before rapid drying begins.
5. Open Time Management
A shorter, controlled open time (e.g., 10–15 minutes) allows adjustments but transitions quickly to the drying phase.
4.2 Strategies Using HPMC in Fast-Drying Tile Adhesives:
1. Using Low-Viscosity HPMC Grades:
- Lower viscosity HPMC grades (e.g., in the range of 3,000 – 15,000 mPa·s for a 2% solution) provide less thickening and, crucially, less water retention compared to standard higher viscosity grades (e.g., 40,000 – 100,000 mPa·s).
2. Using HPMC Grades with Modified Substitution (Lower Hydroxypropyl Content):
- The hydroxypropyl (HP) group on the cellulose chain contributes significantly to water solubility and hydration. Grades with a lower molar substitution (MS) of hydroxypropyl tend to have reduced water retention capacity.
3. Reducing HPMC Dosage:
- Less HPMC directly means less water-retaining polymer in the system.
- This is a delicate balance. Insufficient HPMC can lead to inadequate water retention for cement hydration, poor workability, reduced open time, and insufficient wet adhesion and sag resistance. Finding the minimum effective dose is critical.
5. Redispersible Polymer Powder
Redispersible Polymer Powder(RDP) is a spray-dried polymer emulsion (e.g., vinyl acetate-ethylene (VAE), styrene-butadiene (SB), or acrylic) that redisperses in water, forming a flexible film within the adhesive matrix.
RDP plays a critical role in enhancing the performance of fast-drying tile adhesives while addressing the inherent challenge of balancing rapid setting with mechanical strength and durability.
5.1 Core Functions of RDP in Fast-Drying Tile Adhesives
- Enhanced Adhesion Strength: Forms polymer bridges between cement particles and substrates (e.g., concrete, tiles).
- Flexibility & Crack Resistance: Absorbs mechanical stress from substrate movement, reducing crack propagation.
- Water Resistance: Creates hydrophobic barriers, which are crucial for wet areas (e.g., bathrooms).
- Workability: Improves mortar cohesion and anti-sag properties for vertical applications.
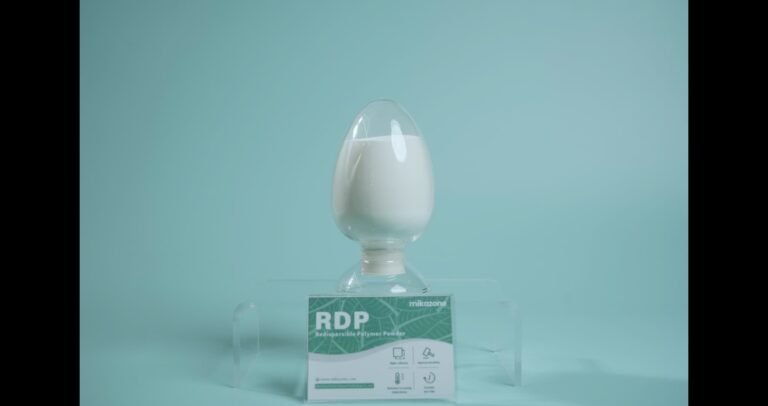
5.2 RDP in Fast-Drying Formulations: Challenges & Solutions
Fast-drying adhesives require rapid water release and cement hydration, conflicting with RDP’s water-retaining nature. Key strategies to resolve this:
Low-Tg Polymer Selection:
- Acrylic RDP: Balances quick setting with high bond strength for premium formulations.
- Styrene-Butadiene (SB) RDP: Accelerates drying due to low glass transition temperature (Tg), facilitating faster film formation and water release.
Optimized Dosage:
- Low-to-Medium Loading (0.5–3%): Reduces water retention while maintaining adhesion. Studies show that 1.5–2% RDP achieves 90% strength development within 6 hours.
- Overdosing (>3%) delays drying and increases cost.
Synergy with Additives:
- Setting Accelerators (e.g., calcium formate): Compensate for RDP’s retardation effect by boosting cement hydration.
- Low-Viscosity Cellulose Ethers (e.g., HPMC): Provide minimal water retention while ensuring workability.
- Desiccants (e.g., calcium oxide): Absorb excess moisture post-setting.
4.3 Dosage & Performance
Typical Range: 3–8% of total dry mix (exceeding 10% may delay curing or reduce compressive strength).
Impact of Dosage:
- Flexibility: A highly flexible tile adhesive formula requires a higher dosage of Redispersible Polymer Powder (e.g., 8% for S2-grade adhesives).
- Adhesion: Optimal at 5–6% for most substrates.
6. Polycarboxylate Superplasticizer
6.1 Benefits of Polycarboxylate Superplasticizer in Fast-Drying Tile Adhesives
1. Water Reduction (20–35%):
Lowers total mixing water, directly reducing the water-to-cement (w/c) ratio.
2. Enhanced Particle Dispersion:
Breaks cement agglomerates, exposing more surface area for rapid hydration.
3. Controlled Rheology:
Improves workability at low w/c ratios without delaying setting.
6.2 Formulation Strategies of Polycarboxylate Superplasticizer in Fast-Drying Tile Adhesives
1. PCE Selection & Dosage
- Dosage: 0.1–0.5% (by cement weight).
- Form: Powder PCE is preferred over liquid for dry-mix adhesives.
2. Synergy with Key Components
Cellulose Ethers (HPMC): PCE counteracts HPMC’s viscosity buildup and maintains workability at low HPMC dosage (e.g., 0.1–0.2%).
Redispersible Polymer Powder (RDP): PCE improves RDP film distribution and enhances early adhesion without retarding drying.
Accelerators (e.g., Calcium Formate): Combine with PCE to offset residual retardation and boost 24h strength by 30–50%.
Summary
Fast-drying tile adhesive enables rapid installation by significantly reducing setting time and moisture release, allowing grouting/walking within hours. This accelerates project timelines, minimizes downtime in high-traffic areas, and reduces tile slippage risks.
For optimal performance, quality additives are critical. Mikazone supplies premium HPMC (for controlled water retention), RDP (enhancing adhesion/flexibility), and Polycarboxylate Superplasticizer (for water reduction and strength) to elevate your formulations. We also offer custom formula development and existing recipe optimization to achieve specific performance targets. Contact us to enhance your fast-drying solutions!